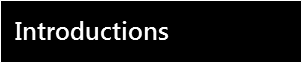
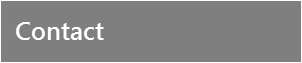
|
Introduction
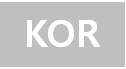 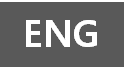
1. Pulsating Heat Pipes (PHPs)
Recently, heat flux dissipationrates have risen to several hundreds of watts per square centimeter because
processor chips and electronics have become smaller and more densely packed. To
effectively transfer heat from the heat source and remove hot spots, we need
highly effective cooling systems. Among various types of heat transport devices,
heat pipes, a kind of passive thermal control device, are one of the most
efficient devices. Although wicked heat pipes
are a proven and widely used technology, manufacturing the complex and
miniaturized wick structure for microelectronic applications is very difficult. The pulsating, or oscillating, heat pipe was suggested to overcome these
drawbacks. The diameter of the tube
of a pulsating heat pipe is designed to be small enough that a slug-train unit is
formed by capillary action. Heat is transported from the evaporator to the
condenser by means of self-excited oscillations of the liquid slugs and vapor
plugs without the need of a wick structure. If this thermal conductor is made flexible, it can be used as a cooling solution for
flexible displays, solar cells, artificial satellites, and
other future devices.
|
 
2. Air-assisted Impinging Jets
Liquid impingingjets are most efficient at cooling small local hot spots such as computer chips
or larger areas. A method of
enhancing the already high heat transfer rate of liquid impinging jets by
injecting air into the liquid flow has been investigated, which is called the air-assisted
jet. This is easily implemented by an air
flow path attached at a point upstream of the nozzle and other inexpensive
equipment such as an air compressor and a flow controller.
This simple implementation allows for the flow rate to
be quickly and easily controlled. This
method is also environmentally
friendly since it doesn¡¯t make use of any chemical substances.
One of our main contributions is a correlation for
predicting the air-assisted jet Nusselt number over a wide range of parameters.
We also optimized the air-assisted jet based on the
two-phase pumping power. The
optimal operating point for any pumping power level can be found.
In addition it was found that the liquid-only jet is optimal when pumping power is low and the jet
diameter is large.
|
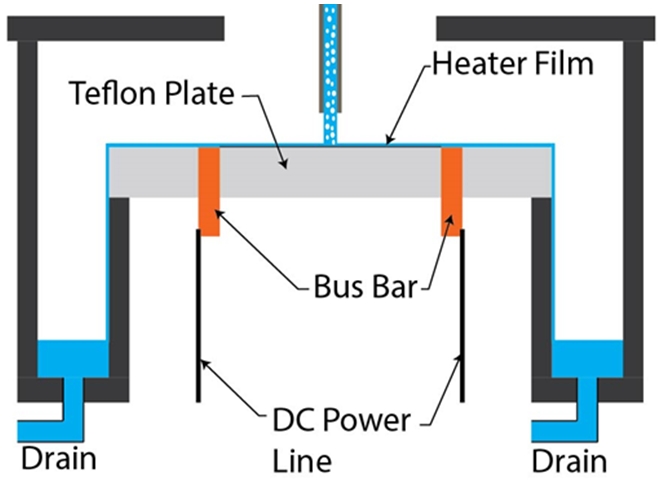 
3. Critical Heat Flux (CHF) Mechanism in Pool Boiling
Critical heat flux (CHF) is the maximum heatflux at which nucleate boiling sustains high cooling efficiency. Determination of CHF mechanisms has been
hampered by lack of access to the local wall heat transfer distribution along
with the inability to visualize the bubble motion in detail. The objective of
this work is to obtain local temperature and heat flux using an IR-based
measurement technique in pool boiling. Using the IR technique, local
temperature and heat flux can be obtained. The wetted area fraction (WF), the contact line length density
(CLD), the frequency between dry out events, the lifetime of the dry patches,
the speed of the advancing and receding contact lines, the dry patch size
distribution on the surface, and the heat transfer from the liquid-covered
areas were measured throughout the boiling curve. Quantitative analysis of this
data at high heat flux and transition through CHF revealed that the boiling
curve can simply be obtained by weighting the heat flux from the liquid-covered
areas by WF. CHF mechanisms proposed in literature were evaluated against the
observation.
|
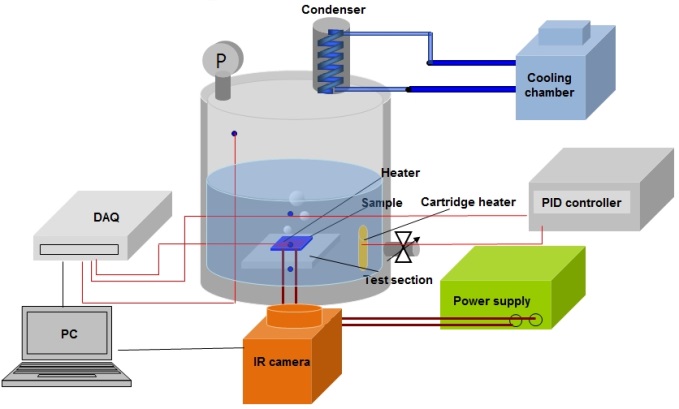 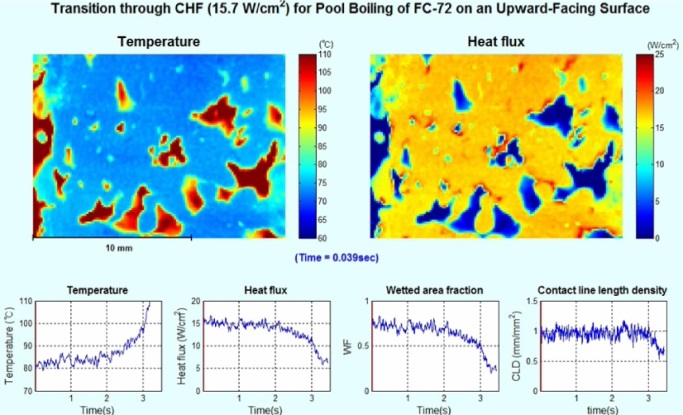
4. Topology Optimized Heat Sink
A heat sink is a cooling device that extend the heat exchange area through the fins and has been widely used to cool high heat flux electronics. However, due to the miniaturization of electronic devices, the space for the heat sink becomes smaller and more complicated. As a result, it becomes difficult to propose an optimal shape of a heat sink with fixed shaped fins, and there is a performance limitation. We are studying for applying the topology optimization method on designing heat sinks to propose an optimum shape of a heat sink that exceeds the performance limitations of convectional heat sinks by eliminating the limitation of shape. The topology optimization method gives the ultimate degree of freedom to the shape of the structure by dividing the computation domain into a number of elements and defining the presence of the structure in each element as a variable and makes the shape of the structure change itself in the direction of optimizing the object function for given condition. We already proposed an optimum shape of natural convection heat sink that satisfies the shape and heating conditions of the system using the topology optimization method. We are going to apply the topology optimization method to various cooling devices such as forced convection heat sink, heat sink in heat exchanger, to provide the optimum cooling devices.
|

|
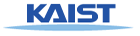 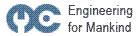 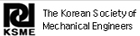 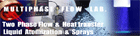 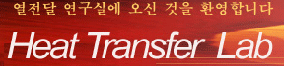 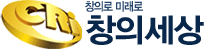
Capyrigt(C) Applied Heat Transfer Lab. Department of Mechanical Engineering, Korea Advanced Institute of Science and Technology
Room# 3116, 335 Gwahangno (373-1 Guseong-dong), Yuseong-Gu, Daejeon, 305-701, Republic of Korea. Tel.+82-42-350-3083 Fax.+82-42-350-8207
|